
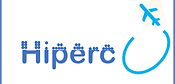

Prior Art

Literature studies have shown that SiC nanopowders can be dispersed into molten aluminium alloys by using ultrasonic dispersion.
Multiple mechanical benefits of the use of nano-sized filler materials, compared to their micrometer sized alternatives, have been demonstrated :
​
Improved tensile and fatigue strength,
Improved stiffness,
Improved fracture toughness,
Decrease of the elongation at break



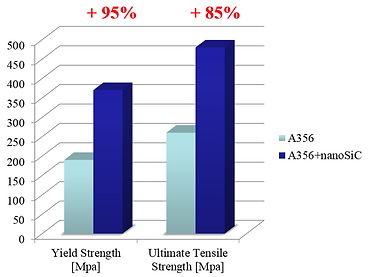
University of Wisconsin
The upscaling of this liquid metal route process is hard and difficult, that’s way a dry mixing route has to be defined and optimized.
Project Objectives
The HIPERCO project has the following objectives:
​
To prepare a new nanocomposite powder by using AS series aluminum alloy powder and laser-pyrolyzed silicon carbide nanoparticles with a long term stability and particles cohesion.
To upscale the preparation of the nanocomposite powder in order to reach a production capacity of tons per year.
To demonstrate that the nanocomposite powder can be used as raw material for the build-up of massive 3D parts, usable especially in the aerospace field.
To obtain a 20% gain in mechical strength and hardness for the nanocomposite parts in comparison with parts made of standard AS series Al alloys.
To prove the industrial scale feasibility of aluminium chips into highly valuable powder using a close loop process.





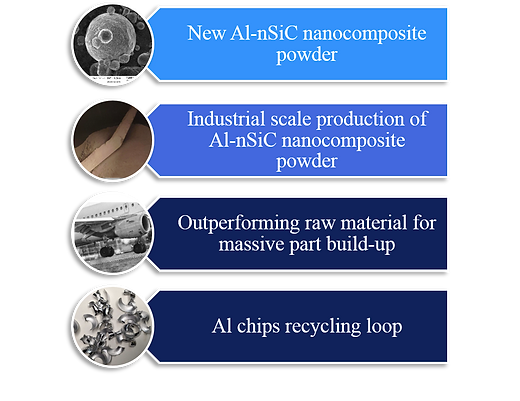
HIPERCO Main tasks
In order to fulfil the HIPERCO challenging goals, strategic project partners, covering the complete value chain are represented in the project. Due to the high TRL level aimed at, the project is driven by industrial partners involved in powder production (Nanomakers and Mecachrome), additive manufacturing tools (Renishaw), and component production, testing and qualification (Safran Data Systems, Mecachrome), and supported by two research partners that are specialized in powder production and handling (CEA Grenoble) as well as additive manufacturing and mechanical testing (KU Leuven).
